Hope Cranks – The wait is over
Hope Technology have a habit of taking their time to make sure their products are bang on, the new cranks are no exception to this rule. It’s not marketing hype or buzz building, this is simple. The guys in Barnoldswick don’t want any product that goes out of their door coming back through it. The press release says ‘Hope Crank’, their seat post wasn’t rushed and that landed the name Eternity so it’s anyones guess what these will be called, answers on a postcard…
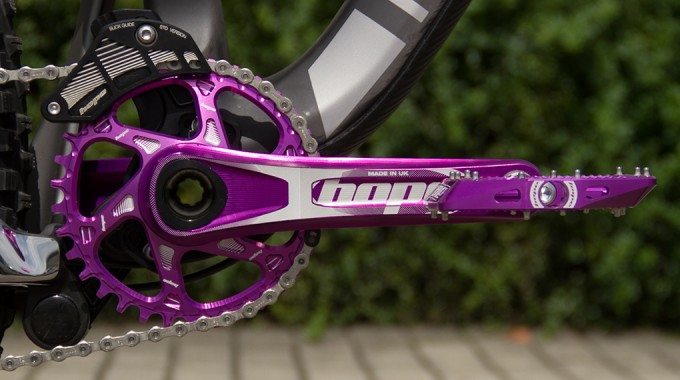
After hearing that Hope were working cranks two or more years ago now it was at Eurobike last year we saw the nearest version of these now production cranks. In Friedrichschafen we were told November but in true Hope style a last minute decision put that back until now, more on that later. The Lancastrian recipe of CNC machining a forged lump of alloy has been honed even further with these new cranks. In the same way their hubs are made Hope have gone to the trouble of designing a forging to be machined. Between the forging and the finished part are a lot of digits and coordinates but hewn from 7000 series these cranks are quite the work of art.
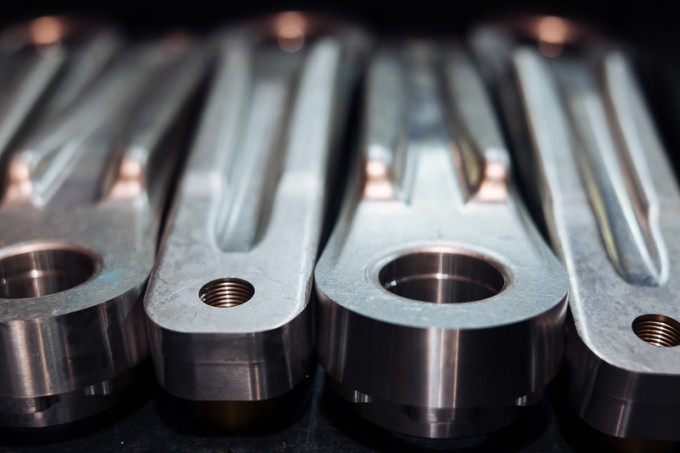
THE CRANKS
This is one of the largest production parts Hope make and as with all of their parts the machining is well thought out. Getting the cranks in our hands they have a purposeful feel, the 30mm axle should add a good amount of stiffness and keep the power transfer direct. A black anodised finish laser etched with the Hope logo is something we are now used to and it looks spot on. The cranks come in 165, 170 and 175mm lengths to cover all riders and should deliver the same solid build quality a product with such a lengthy development embodies.
That development has seen Hope go through Finite Element Analysis to make sure these cranks are up to the job. Without going into equations this is basically a super detailed look at how each part of the crank performs under different stresses.
once it’s out the door, we don’t want it back
The cranks have been tested on a load of different bikes with Adam Brayton trying his best hucks to flat in the pursuit of perfection. Hope have also setup a new mechanical test facility in which the cranks have been put through their paces with thousands of cycles of pedalling stress and bending to make sure they will last. Hope have gone to town, reinforcing the philosophy of “once it’s out the door, we don’t want it back”.
Talking to Hope at Eurobike a decision had been made to move away from the polygon interface we have seen on E13 cranks in the past and develop their own splined system. The system is patent pending and works the same for the drive side and non drive side arms, here’s how.
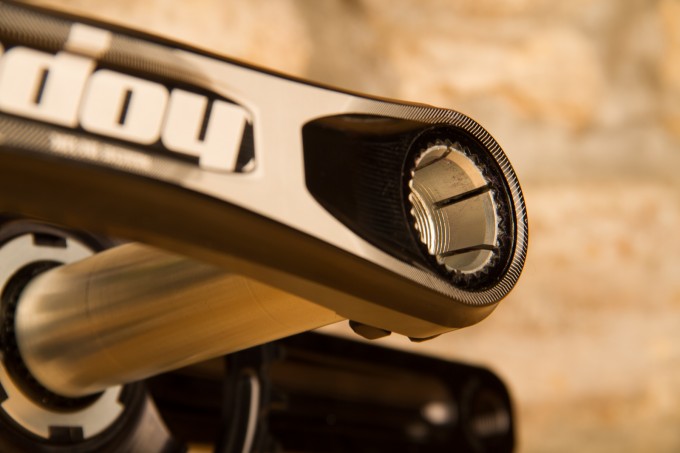
FITTING
The first thing that stands out is the cuts through the splined end of the axle, the purpose of that will be come clear but at the inside end of the splines are small ramps that the arms tighten against. With the cranks pushed through the bottom bracket the non drive side arm slots onto the axle with a reassuringly tight tolerance and the threaded collar, that works in a similar way to previous XTR cranks, wound back as close to the crank as it goes.
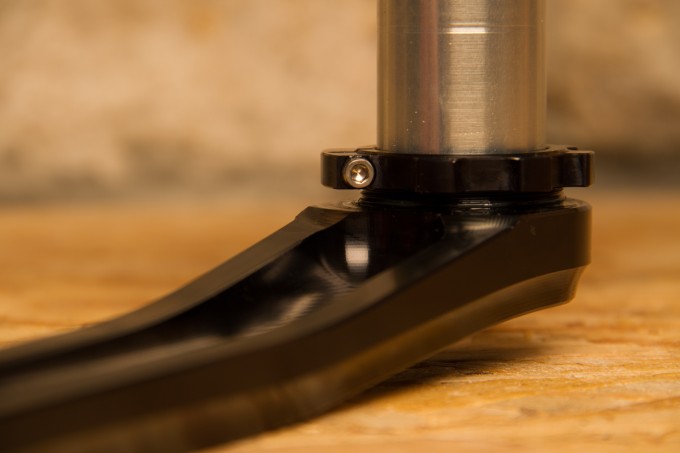
Once in place the tapered nut threads into the middle of the axle using the tool provided expanding the flanges between those cuts into the internal surface of the crank arm, things are getting secure. Then the final piece is a bolt, via a 10mm allen key this locks everything in place wound to between 17 and 20 Nm into the tapered nut. Once that is done the collar is wound out against the bottom bracket bearing and locked in place with a 3mm allen key.
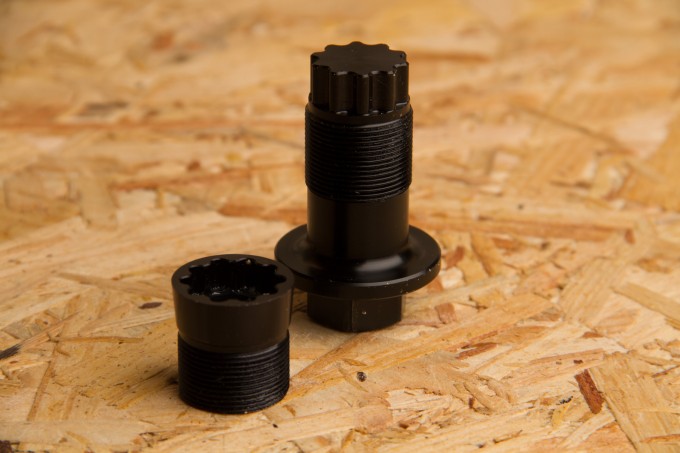
The clever thing about this system is that it allows for wear and should in turn add longevity to this investment. We haven’t experienced this problem very often but if cranks become slightly loose the splines inside the crank can wear, once they have no matter how tight you do up the external bolt they will still be loose. The combination of the expanding axle and ramped ends to the axle splines means that if things get worn you can loosen everything off re-tighten and they should be as good as new. We will have to give them a lot of testing to prove this works but the principle seems sound and Hope must think it is to have applied for a patent on it. Crank removal is a simple affair, engaging the lockring with the flat wishbone shaped tool between that and the bottom bracket. Winding the locking against the tool lifts the crank off the axle and the drive side can be removed.
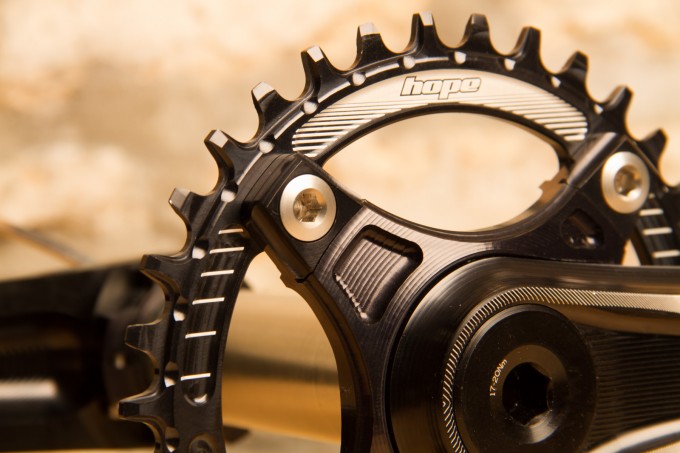
The rest of the crank is what you would expect from Hope, some of the best looking CNC machining you will find. Hope don’t go for a smoothed finish aiming to look like a polished forging, you can see where the CNC tool has been and visually that adds a little something. The cranks are designed to run with pedal washers, again a thought of longevity.
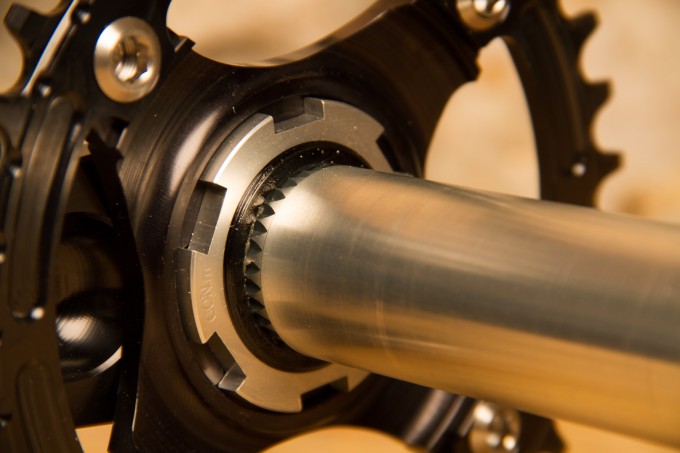
CHAINRINGS
As we saw at Eurobike Hope have been working on a spider less chainring that can be fitted to their new cranks but they do also have a spider option so you can run what ever chainring you like, so long as it’s 104 BCD. There are a few tools included with the Hope cranks and the aluminium one pictured here locks the spider or spiderlesss chainring in place. There’s no cir clip or anything else to hold it in place but a recommended load of 60Nm should take care of that. We are due to get a spider less ring early next week so when that arrives we will fit that and give it a spin.
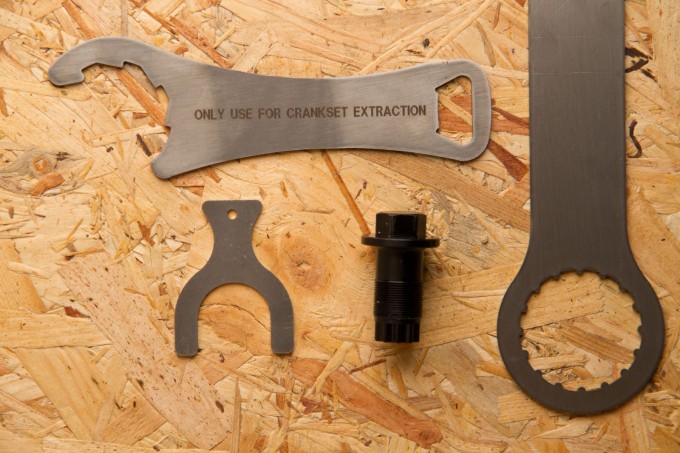
Tools
As the Hope cranks have their very own and new system there are a couple of specialist tools you will need to fit and remove them. The far right tool is a standard bottom bracket tool, the cranks run a 30mm axle so one of Hope’s own BB’s is also needed to get things spinning. The ‘wishbone’ tool is used when the cranks are removed from the axle and this sits between the BB and the collar that is unwound with the middle tool to remove the non-driveside are. The black tool with a 19mm bolt head is for fitting and removing the tapered nut that expands the splines of the axle.
The cranks will be shown at Core Bike at the end of this month and will be in shops after the show.
Prices
Arms, Axle and Spider £245
Arms and Axle £215
Spider £40
Spiderless Retainer Chainring £55